About Us
Avestronics Industrial Sales and Services Inc. is committed to delivering the highest standards of quality, in terms of our People, Products and Services (PPS). We are committed to business excellence as guided by the following principles:
Our People's Values
Service Standards
Commitment to Quality
Communication
Continuous Improvement
Our Guiding Principles:
Our People's Values
Transparency, Honesty, Trust, Flexibility and Integrity are the core values that we want to implement to our people in order to achieve good rapport within the management and our employees; to be able to deliver good products and services to our clients.
Service Standards
The company shall deliver products and services that meet the requirements set by our customers and the applicable regulatory authorities related to our business. We shall at most possible comply with all the established procedures, quality standards, safety standards and regulations.
Commitment to Quality
The company will perform to the best of our capabilities at all time. We endorse the core values of our people as the foundation of our company in approach to the quality of our commitment.
Communication
At all times we will communicate, and in most possible way, the company is encouraging an open communication between the Management and our employees, our clients, suppliers and partners as part of the culture that the company wants to cultivate. We shall report incidents to the relevant parties including reportable issues or errors and make necessary actions. And to balance it, we encourage sharing of quality information as part of having a quality communication.
Continuous Improvement
We strive to grow; to learn and improve will never be out of our Company’s culture. Our top four (4) quality policies namely, OUR PEOPLE’S VALUES, SERVICE STANDARDS, COMMITMENT TO QUALITY, COMMUNICATION will serve as the driving framework to instill quality culture of excellence, innovation, creativeness and continuous improvement. We shall maintain appropriate controls and reviews from time to time to check our set goals.
History
In 2002
Avestronics Industrial Trading started and concentrated mainly in supplying Preventive and Maintenance Chemicals as well as household chemicals with Industrial and hospitality industries as their clients.
In 2004
Avestronics saw the need to expand its products from Preventive & Maintenance and Household chemicals to Fire Fighting and Safety as well as Environmental Products. Then added services like Waterproofing, Epoxy painting and Air-con cleaning to name a few as part of its expansion. Eventually Avestronics Industrial Trading became Avestronics Industrial Sales and Services.
In 2006
Avestronics went into Importation. Hydrazine Hydrate, Aluminum Sulfate, Ammonium Hydroxide and Poly Aluminum Chloride are the major products that they import as well as Fire Fighting Equipment, Safety and Environmental products like Lamp Crusher and other Engineering equipment like Vacuum Circuit Breaker (in small, medium, large size), mixing tees, special pipes etc which they cater to Power Plant Industries, Water District and other industrial companies.
In November 2007
Avestronics Industrial Sales and Services was registered in Securities and Exchange Commission (SEC) with the name; Avestronics Industrial Sales and Services, Inc. with registration number CS200717808. This time Avestronics welcomes its horizon in the field of water filtration through the help of its supportive partner suppliers abroad. Avestronics now caters to many industrial and institutional companies in the Philippines with Power Plants, Water Districts and Hospitality industries as their major clients.
In 2010
Avestronics Industrial Sales and Services, Inc. introduces its trucking services in the market which caters to NCR, Luzon, Visayas and Mindanao.
Environmental Awareness
Environmental Management Plan
(on Land, Water, Air and People)
1. INFORMATION / AWARENESS
Employees who are occupationally exposed to, or who handle hazardous waste must receive initial hazardous training. They must be initially informed with First Aid Procedures and other Precautions before they begin to work with hazardous waste. At a minimum, the training must be designed to ensure that personnel are able to respond effectively to emergencies. New employees will require constant supervision (by trained personnel) until they have completed training.
3. CONTAINER MANAGEMENT
- Containers must be protected from rain and other weather elements.
- Containers must be closed at all times except when it is necessary to add or remove waste.
- If funnels are used for adding waste to containers, they must not be left in container openings.
- Do not overfill containers. In a 55 gallon drum, leave 3-4 inches of space at the top of each container to allow for heat expansion. During the summer, products should have 6 inches of space at the top of each container to allow for heat expansion within the container.
- Do not stack drums more than 2 high. All drums should be stored on serviceable pallets and protected from being overturned.
- Do not allow residue to accumulate on the top of containers.
- Inspect containers at least weekly for deterioration, leaks, heat expansion, dents and excessive rust.
2. MATERIAL SAFETY DATA SHEETS
Material Safety Data Sheets (MSDS) must be available at all work locations where a hazardous chemical will be used. The material safety data sheets should be in a specified area, well marked and all employees should be encouraged to read and understand them.
8. MARKING/LABELING PROCEDURES
Containers must be properly marked/labeled upon placing the first drop of hazardous product in them.
(a) Hazardous Waste. Containers must be affixed with a properly completed “Hazardous Waste” label.
9. HANDLING AND TRANSPORTATION
(a) Before transporting or offering hazardous waste for transportation off-site going to the client, a manager or appointed employee in-charge must label the packaging with Batch Number bearing Manufacturer’s name, Material Safety Data Sheet (MSDS), First Aid Measures and Certificate of analysis.
(b) Proper personal protective equipment should be worn if required for the type of property being handled.
(c) Drums should be banded to pallets when possible to prevent them from tipping over during transportation.
10. SPILL REPORTING PROCEDURES
If spill took place, immediately notify the Duty Manager. (Only if applicable). We are only into storage. After Sea Port, only one day storage and after that the goods will be delivered to client the next day.
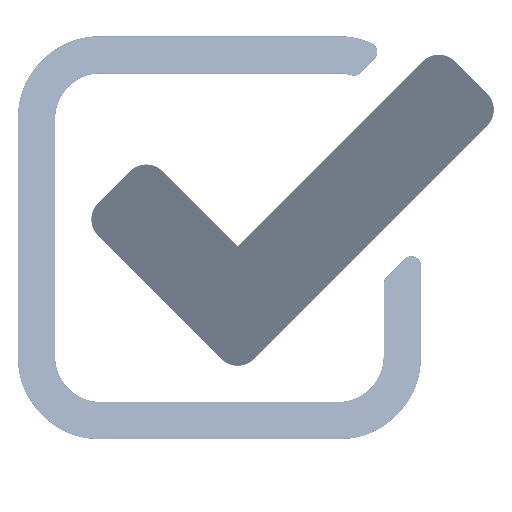
Manager Responsibilities
- Ensure the site is managed in compliance with all laws, regulations and operating instructions.
- Ensure the site is kept neat, clean and orderly.
- Ensure proper marking/labeling procedures are used on all drums.
- Monitor the type and quantity of products at the site.
- Ensure that waste streams are accumulated in separate containers and are not mixed together.
- Ensure proper containers are used for the accumulation of used products and ensure storage compatibility.
- Ensure a spill kit is maintained at the SAP.
- Ensure that appropriate signs have been posted.
- Ensure that containers are kept closed except when being filled.
- Maintain a record system for Material Safety Data Sheets, Hazardous Waste Management, copies of Certificate of Analysis etc.
- Ensure all spills are reported in accordance with existing procedures.
- Ensure employees are properly informed for awareness of Precautionary measures, First Aid etc.